Turbulent Flow
The geometry of the “V” type elements
like the one in the photo above is without a doubt the most successful in the world market due to the multitude of applications that are carried out in different unit operations in the industry such as mixing, dispersion , stirring, homogenization, extraction, and absorption among others. These operations are carried out mainly when the fluids are of low viscosity, whether they are gases with gases, gas/liquid and liquid/liquid, where the common factor is TURBULENT FLOW.
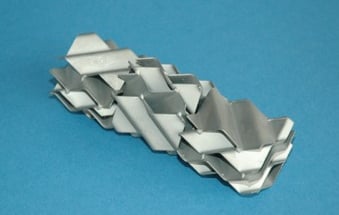
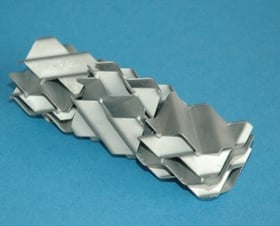
when having “Gas Mixing”, it is very important to have a mixing element geometry that homogenizes efficiently and with practically no pressure drop. This requirement occurs mainly in short spaces where gases with large differences in density and/or temperature circulate and that can form layers of stable flows, when velocities are slow.
The typical sizes of these mixers are those whose applications refer to large industrial facilities.
There are also less sophisticated and more economical elements (in small diameters) that can fulfill the function described above in places where space is not restricted and there is freedom of length, I am referring to the SMH type (twisted slat).
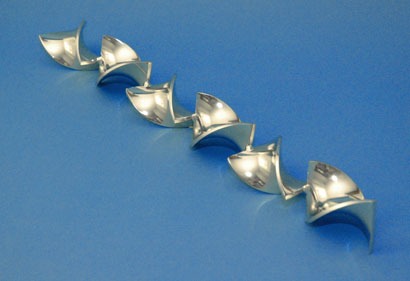
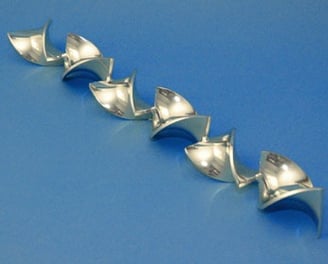
“SMH” type mixing element, very useful in low viscosity mixing operations.
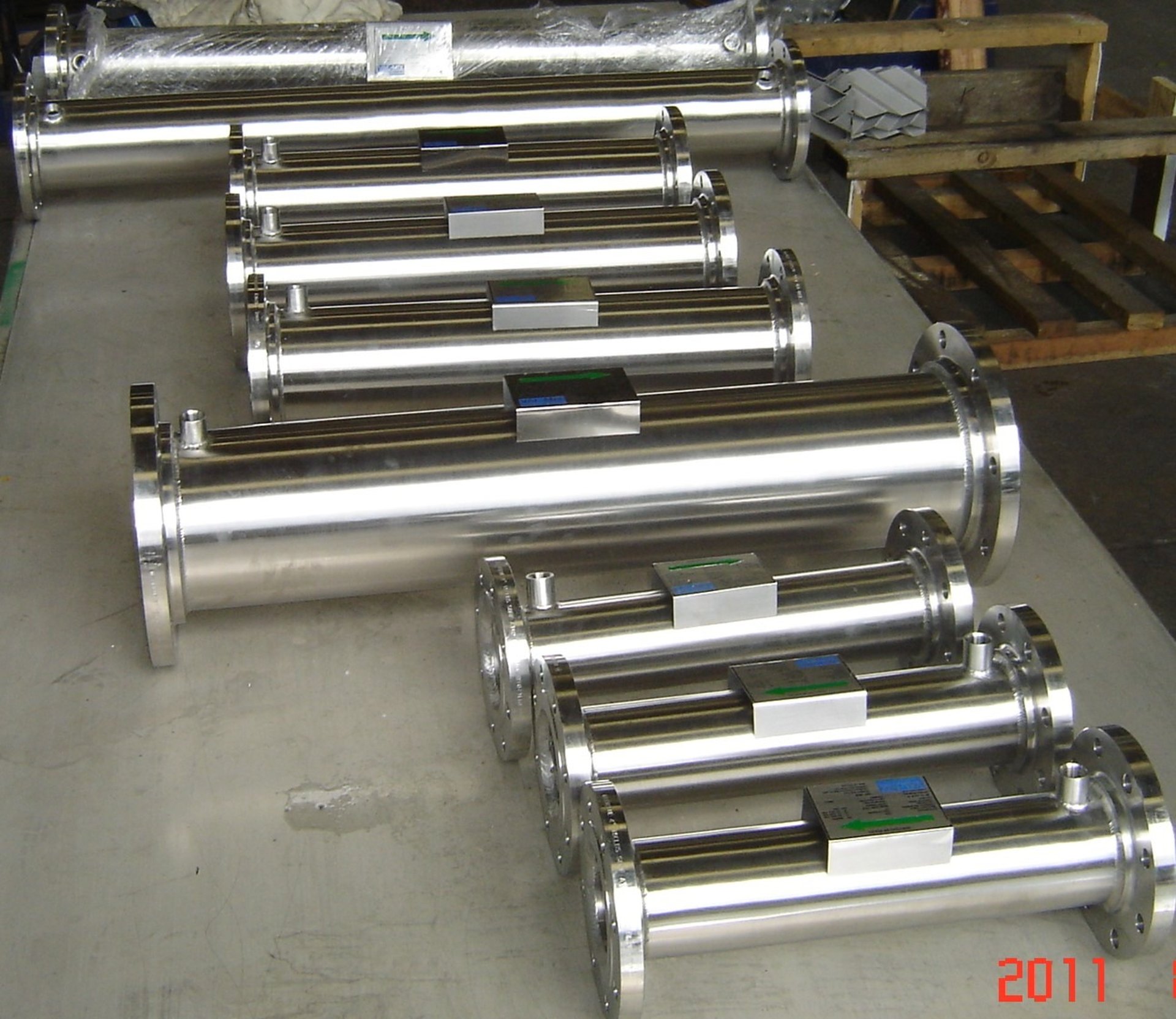
APPLICATIONS
Mixing natural gas with steam before the catalytic reformer in ethylene / propylene plants.
Mixing natural gas with propane in steel mills.
Mixing of primary and secondary air temperatures including steam with diesel or kerosene before the burners.
Homogenization of temperature and relative humidity in drying plants, in the production of paper, textiles, or in automotive paint drying warehouses.
Homogenization of temperatures and densities of steam coming from different boilers before the turbines and in the air before the turbochargers.
Mixing of ammonia with tail gases in DeNOx plants.
Large air conditioning installations in buildings, etc.
In the topic of "Mixture of gases with low viscosity liquids," the goal is to maintain a very high concentration of one phase within the other. This is only achievable when there is excellent interfacial contact area between both phases. Besides the contact surface, the geometry also plays a crucial role in forcing the phases to continuously contact each other.
A modern application of these technologies is the use of ozone instead of chlorine in water treatment processes. Ozone is more reactive than chlorine, capable of destroying the cell walls of bacteria, and does not require recovery or inhibition like chlorine does. Chlorine is highly corrosive and polluting, which increases the cost of the process. The effectiveness of ozone is achieved through the constant breakdown and uniformity in the size of the gas phase bubbles dispersed in the liquid phase intended for disinfection.
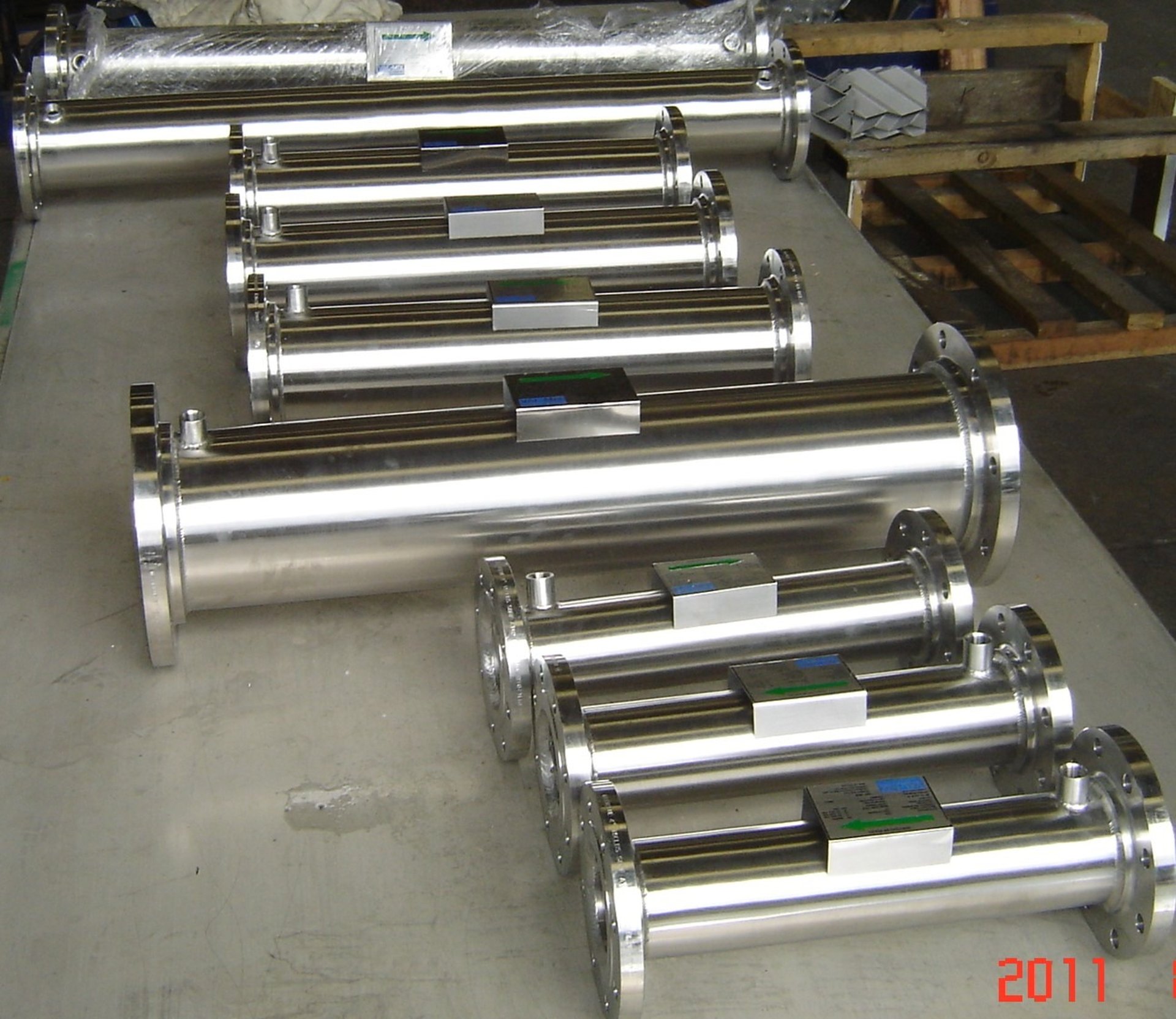
APPLICATIONS
Increase in the area and time of contact between a gas and a liquid as in hydrogenation, oxygenation, alkylation, phosgenation, etc.
Ozonation, chlorination in the sterilization of drinking water.
Carbonation of drinks with CO2.
Elimination of flavors and oxygen in oils, edible fats, or chocolates, through exhaustion with steam or N2 or CO2.
Desorption of CO2 with air, in deacidification processes. • Dissolution of H2, NH3, SO2, Cl2, HCl in water.
Oxygenation in well water, fish farms, production of drinking water.
Chimney gas scrubbers, removal of HCl, SO2, H2S and others.
Natural gas drying with triethylene glycol.
Sweetening of natural gas with amines or CO2, etc.
Reaction Application Design (Oxidation)
In this example, we observe a special design for a reaction application (oxidation) where empty spaces are maintained. The lengths of these spaces are calculated based on the gas flow speeds within the liquid and the required reaction time. This design allows for a reduction in the costs of the mixer-reactor without sacrificing efficiency.
It is crucial to note that we can predict and maintain the size of the bubbles, breaking them down to the most convenient diameter under various operating conditions. This optimization increases mass transfer by enhancing the interfacial contact between components, thereby providing an excellent opportunity to optimize the process and improve operational efficiency.
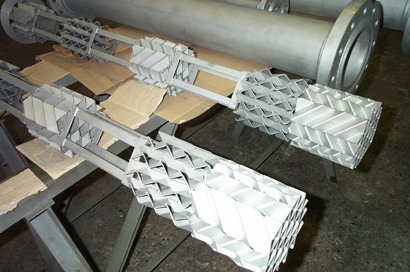
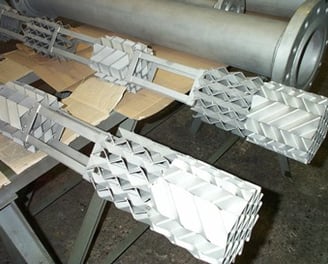
Mixing of Liquids with Liquids
There are two scenarios for liquid-liquid mixing: those that maintain turbulent flow and those that transition to laminar flow. This section will focus on the former, while the latter will be analyzed in the corresponding section.
Typically, the components to be mixed are soluble in each other and require a very short space to achieve a high degree of homogeneity. This homogeneity depends on the specific application of the mixture and the concentration of one compound in the other. For instance, mixing components in a 50/50% ratio is easier than mixing one component in 1,000 parts, such as some anilines in various petroleum products for easy identification.
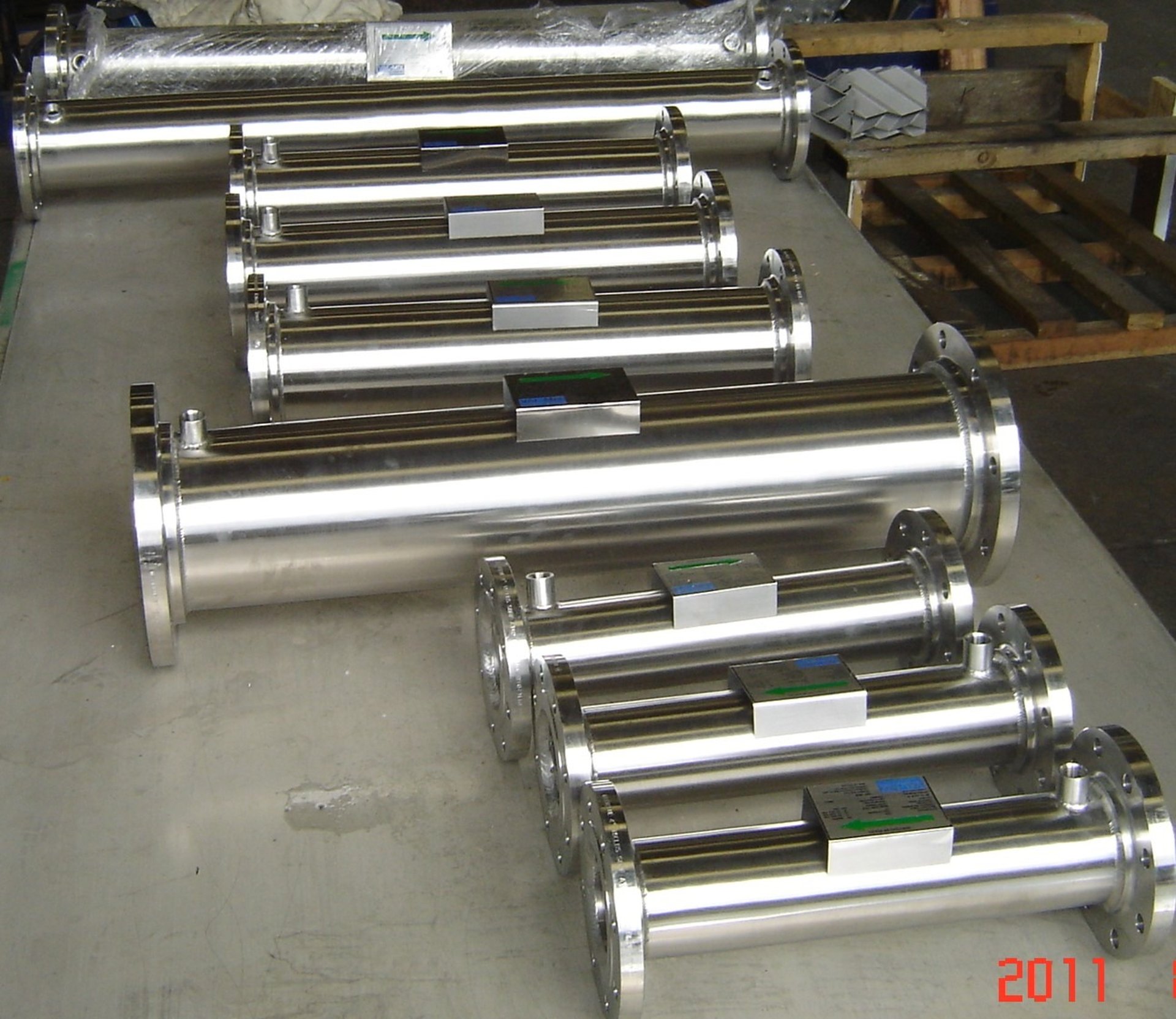
APPLICATIONS
Neutralization of acidic or basic currents, and pH control.
Dilution of concentrated products in water.
Dispersion of polymers and small solids in the paper industry, or water treatment (flocculation).
Mixtures of additives or inhibitors in chemical streams.
Homogenization of streams to obtain truly representative samples of the quality of the mixture (crude oil transportation lines).
Injection and mixing of water for crude oil desalination.
Homogenization of oils of different grades with additives, etc.
In the photo, you can observe a short mixer with only three high-efficiency elements designed for an instantaneous chemical neutralization reaction of a base with phosphoric acid. The entire construction is made from 316-L stainless steel.
Solutions
Process equipment expertise tailored to your needs.
our Offices
Kansas City, Missouri
© 2025. All rights reserved. Val-Mix USA
State of México, México