Laminar Flow
Static Mixing Technology with "X" Type Geometry
The "X" type geometry element pioneered the technology of static mixing, initially utilized to homogenize viscosity and temperature across the cross-section of a polymer fiber thread. This thread must solidify as it descends from the extruder to the winding spool without breaking. Achieving this requires the avoidance of parallel tensions in the falling thread, which would otherwise result in "several currents with different degrees of polymerization, and therefore viscosity and tension, flowing in parallel," leading to thread breakage before reaching the winder.
To ensure a single homogeneous stream in viscosity and temperature before the thread exits the extruder, "X" and "LMXR" mixers are employed. These operations are typically conducted in processes where high-viscosity products, such as high molecular weight polymers, are mixed with additives, colorants, and other components. In these applications, a flow with a low Reynolds number predominates, characterized by LAMINAR FLOW.
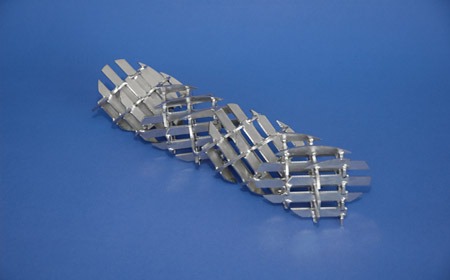
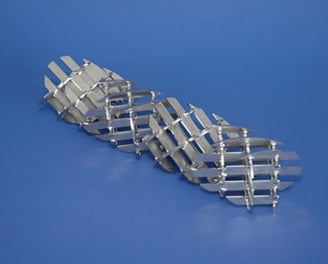
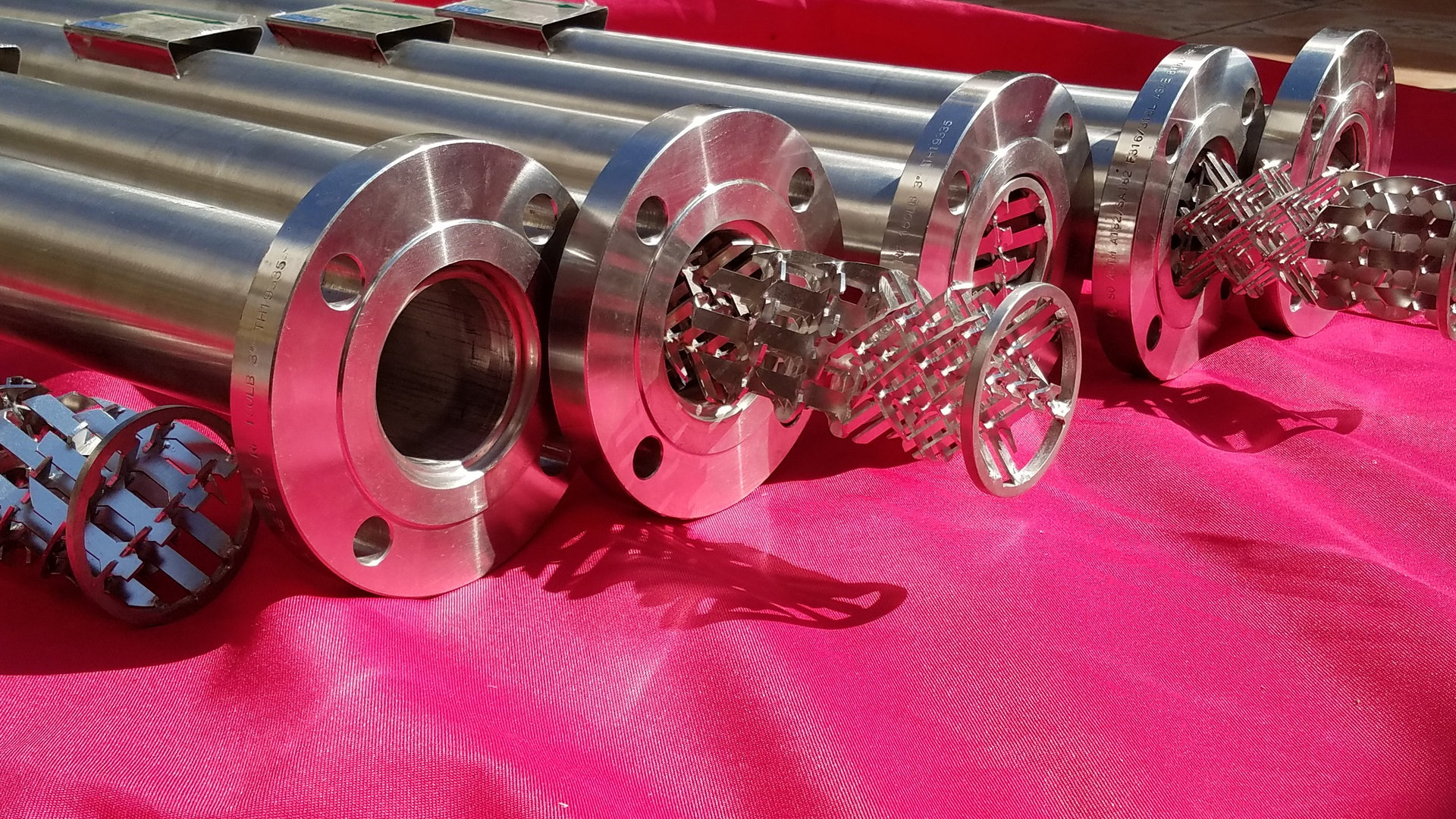
Applications
Photographic Emulsions: Homogenization of photographic emulsions.
Plastic Films and Laminates: Homogenization of plastic films and laminates.
Cosmetics and Shampoo: Homogenization of cosmetics and shampoo.
Epoxy Resins: Mixing epoxy resins with hardeners.
Pigments with Resins: Mixture of pigments with resins.
Polymer Blends: Mixing TiO2 masterbatch in polymer blends.
In the photo, you can see a tiny mixer element used to homogenize synthetic fibers for the textile industry, just before the exit extruder. The number of elements is determined based on the maximum allowable pressure drop and the degree of homogeneity required by the process.
"X" type mixers are also employed for dispersing liquids with significant viscosity differences between them. These operations are typically performed when the streams have viscosity differences of up to 1000:1. During this process, the initial elements continually divide the layers of the low-viscosity additive until they become increasingly finer, with the differences being reduced by dissolution along the mixer.
When the low viscosity additives do not dissolve in the low viscosity components, they can be dispersed by breaking the dispersed phase into droplets of a size most convenient for the process. Similar to gas-liquid mixing processes, the droplets of the immiscible additive break up to a predictable and controllable size, which depends on the differences in viscosity, the length of the mixer, and interfacial tension.
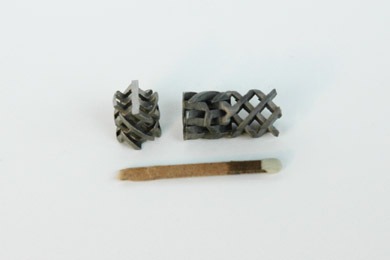
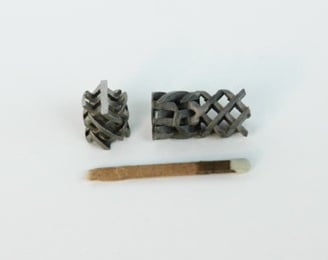
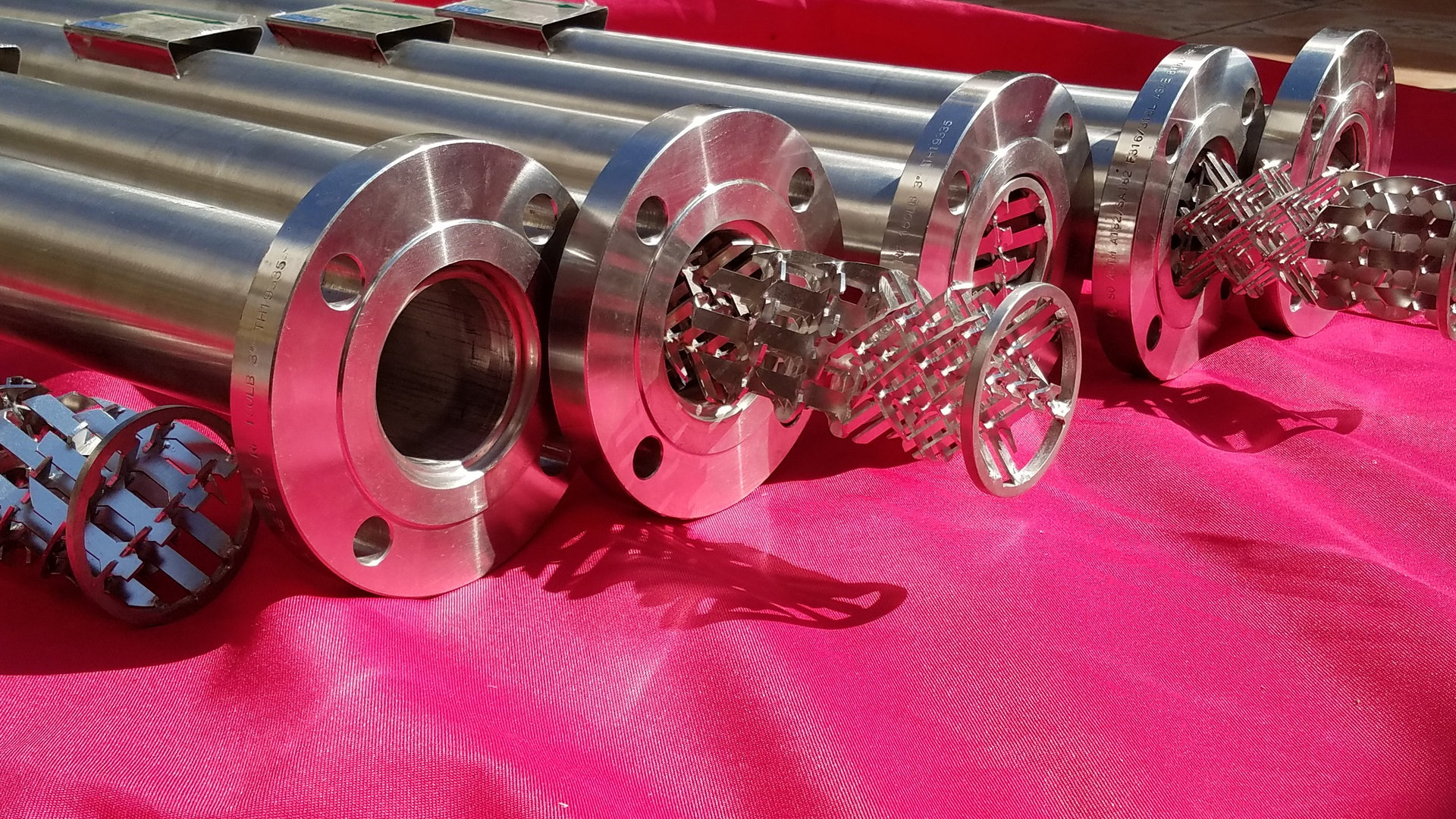
Applications
Viscose and Dyes: Mixing viscose with dyes.
Viscous Flocculants: Diluting viscous flocculants in water.
Molasses: Diluting molasses with water.
Depletion Agents: Dispersing depletion agents in polymer solutions for devolatilization of monomers.
Low Viscosity Additives: Mixing low viscosity additives in polymers, such as mineral oil in polystyrene.
Polyurethanes with Pigments: Combining polyurethanes with pigments
In the photo, you can observe the continuous change throughout the entire cross-section of the mixer, which homogenizes color, density, viscosity, and temperature. This design significantly enhances the efficiency of heat exchangers with mixing elements inside the pipe. By incorporating these elements, the length of the exchanger can be reduced by up to six times. For instance, if the original equipment required six meters of length to achieve optimal reaction and homogenization in a viscous process, it will now only require approximately one linear meter.
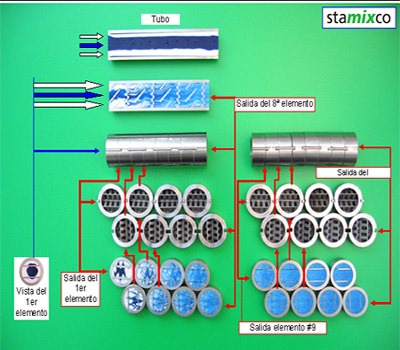
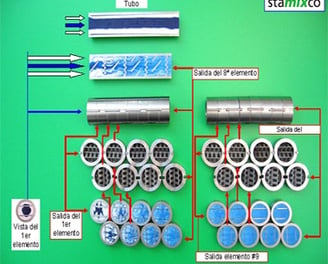
Solutions
Process equipment expertise tailored to your needs.
our Offices
Kansas City, Missouri
© 2025. All rights reserved. Val-Mix USA
State of México, México